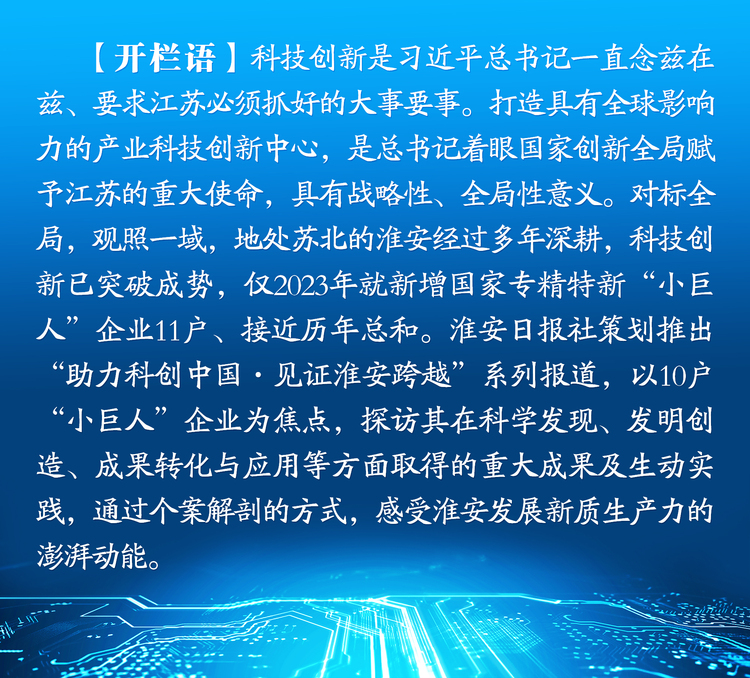
这件事多少出人意料,也令国内业界人士为之一振——
以关注化学综合领域重点研究和前沿进展而知名的国际顶级期刊《英国皇家化学学会》,在其日前出版的最新一期刊物上,刊发了一篇有关双金属催化剂催化二氧化碳与环氧化物开环共聚的论文,论文作者之一竟来自于中国江苏苏北地区一家年产值仅有2.5亿元的企业。
这家企业就是扎根淮安、已跃身成为双金属催化剂研发与生产领域“金字塔尖”的江苏巴德聚氨酯股份有限公司(以下简称“巴德聚氨酯”)。去年,该企业成功入选国家专精特新“小巨人”企业名录。
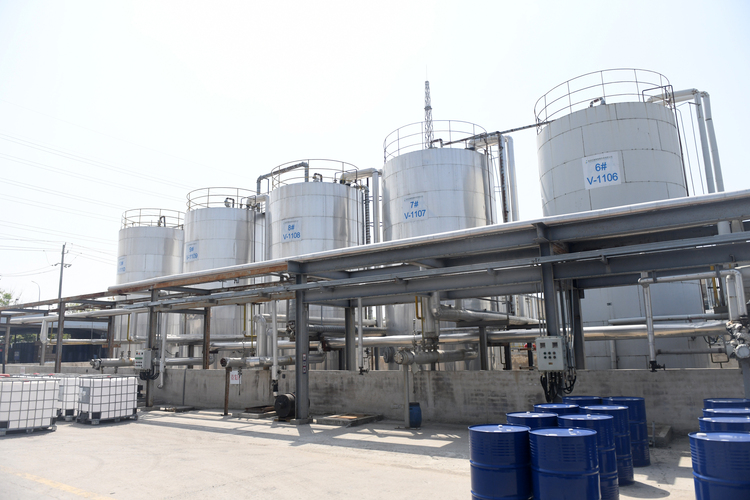
当然,对外行人而言,如果不加以探究,就很难搞明白,上述论文的发表及其所呈现的研发成果到底有何价值,又意味着什么。
通俗地说,在化学领域有一种近乎神秘的力量,它可以精准、高效地引导物质在化学反应中加速运动,从而促使化学反应在尽可能短的时间内得以完成。有了这种神秘力量的加持,既可以提高化学反应速率,又不改变化学平衡,且其本身的质量和化学性质在化学反应前后都不会发生改变。
这种神秘力量就是催化剂,被人们称作工业味精,在现代化学工业中占有极其重要的地位。双金属催化剂是其中一种,在聚醚多元醇的生产中扮演着重要角色。作为有机化合物种类之一的聚醚,是生产海绵泡沫、弹性体制品、密封胶等生活用品不可或缺的原料。
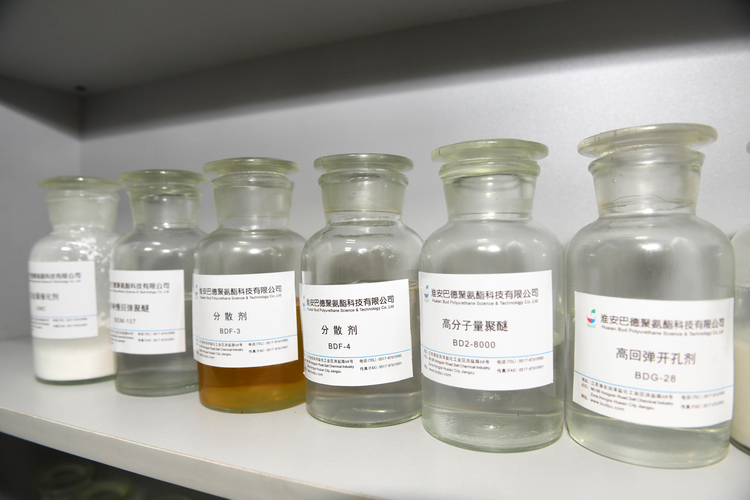
然而,2011年以前,双金属催化剂生产技术一直被国外封锁垄断,国内只能以高价进口双金属催化剂生产的聚醚多元醇。受制于核心原料双金属催化剂的制约,我国国内聚醚生产企业只能采用碱金属催化剂(如氢氧化钾)催化生产聚醚多元醇。与双金属催化剂相比较,使用氢氧化钾生产聚醚存在诸多弊端,比如生产周期长,能耗高,生产工序繁杂,伴随而来的还有大量废水、废渣,产品品质也不佳,等等。
一边是物美但价高,一边是价廉却折腾,无论是放弃前者还是选择后者,都是一种无奈之举。而导致尴尬与困局的根源,正在于技术上被国外卡了“脖子”。巴德聚氨酯的三位创始人既不甘心,更不服气,一场催化剂研发领域的较量就此展开,双金属催化剂生产技术在中国从“0”到“1”的攻坚冲锋随之发起。
查文献、做实验、分析数据,在他们的带领下,研发团队历经无数次从失败到失败,再从无数次失败中一次次从头再来,一次次合力攻关,终于冲破了国外封锁线,成功自主研发出双金属催化剂。
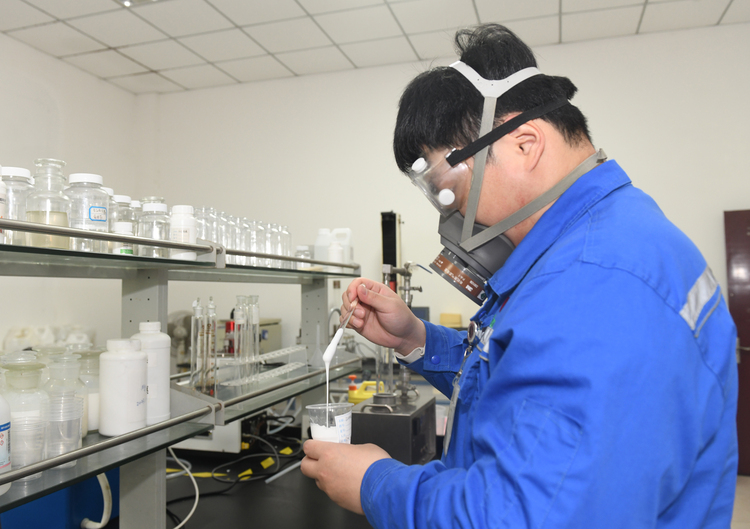
“高效、绿色、节能是双金属催化剂的鲜明特点。”巴德聚氨酯总工程师赵宝成用一组数据进行对比:生产等量的聚醚,所需要的双金属催化剂用量,仅相当于氢氧化钾催化剂用量的1%,且由于双金属催化剂的高活性特性,聚醚多元醇的生产周期由原氢氧化钾催化的30个小时缩短至8个小时,下游企业生产出的聚醚多元醇产品,每吨可节约生产成本500元至1000元不等,产品质量却得到了显著提高。
突围成功,乘胜追击。由于双金属催化剂生产技术被攻克伊始,其生产工艺采用的是间歇法,也就是在化工设备反应釜(一种物理或化学反应容器)中,一釜一釜反复进行投料、生产、出料,产品批次之间波动较大。为改变这一状况,在随后长达7年的时间里,研发团队马不停蹄持续攻坚,并于2018年开发了适用于聚醚连续化生产的双金属催化剂新工艺——连续法生产工艺。
这一生产工艺新发明随即获得了国际专利,同时也引发了聚醚行业的颠覆性变化。“采用连续法生产工艺生产聚醚多元醇,与之前的间歇法相比,生产周期大幅缩短,聚醚产能大幅提升,能耗进一步降低,产品稳定性高,而且自动化程度高,安全系数也得到了大幅提升。因聚醚连续化催化剂的问世,近几年,国内聚醚多元醇产能由2018年的530万吨上升至2023年的760万吨,产能得到了大幅提升。
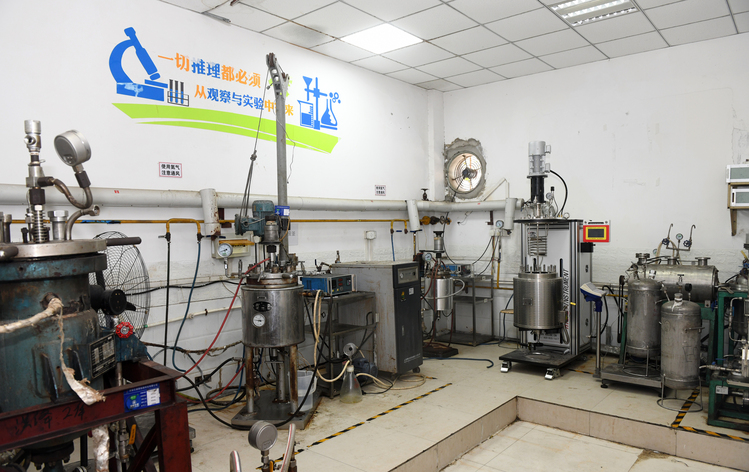
赵宝成告诉记者,2023年巴德聚氨酯的双金属催化剂年销量为34吨,占全国双金属催化剂销售市场份额近80%。也就是说,由巴德聚氨酯自主研发的双金属催化剂生产的聚醚多元醇达百万吨,每年不仅帮助国内聚醚产销企业节约生产成本超10亿元,还为聚醚行业减少固废、废水排放约7万吨,能耗也实现了大幅下降。
毫无疑问,加快培育和发展新质生产力,巴德聚氨酯的科技创新之路才刚刚开始。